If you are in the manufacturing industry, you likely understand that the bookkeeping and accounting look a bit different than it does in other industries. This is because the manufacturing industry has some unique situations not necessarily found in other industries.
Not only do you, as a manufacturer, have the expense of any products that are coming in, there are the expenses incurred while creating the product for resale, as well as the expense of any inventory that is being held until it sells.
As a manufacturing business, you need to take into consideration the cost of goods manufactured, you need to take into consideration your inventory valuation.
Let’s start by discussing the inventory involved in manufacturing.
Inventory refers to the goods and materials that a business holds for the ultimate goal of production or resale.
Since inventory can be one of the largest assets that a business has, it needs to be valued. This means that a monetary value needs to be assigned to the inventory. When it comes to manufacturing and inventory valuation, this isn’t as easy of a process that it in in other industries.
When valuing the goods in manufacturing, you need to take into consideration not only the value of raw materials, but also the value of the work in progress and the value of the finished goods as part of this process.
As well, if there are any ending balances of materials or inventory when the period ends, these must also be properly valued before being recognized.
To further explain, the raw materials, or the direct material inventory, includes all of the materials that the manufacturing company uses in order to make its product. For example, if you are in the computer industry this would include and motherboards, metals, and so on.
These products are typically listed on a bill of materials that you receive, and it will itemize not only the quantities, but the costs of the materials that you are using.
As we discussed in our blog ‘Bookkeeping for Manufacturing Businesses’, perpetual inventory or continuous inventory tracking will keep a running total of what products are coming in or going out via your software program.
The next type of inventory is your work-in-process inventory. This inventory includes anything that is still in the process of being made but has yet to be competed. This inventory is valued based upon how far along the process of being built it is, or how complete it is.
The work-in-process inventory valuation includes the cost of goods that are in production as well as the monies spent to date. This includes not only the raw, or direct materials that have been used, but the direct labor and any overhead that has been applied to date.
Once the work-in-process has been completed, the inventory is transferred into the finished goods inventory.
Finished goods inventory includes the costs that are associated with the completed goods and are ready to be sold but have yet to be sold. As well, the manufacturing costs noted above, whether they be direct or overhead costs, are included in this inventory until the products are sold.
At this stage, the cost of completed goods are now called the cost of goods manufactured, because they are complete.
These manufactured goods will stay in inventory until ownership has actually been transferred over to the customer. When the goods are in transit to the customer, it needs to be determined if the terms of sale are free on board (FOB) shipping point, of FOB destination.
FOB shipping point means that the customer will own the merchandise as soon as it leaves the manufacturer’s loading dock. The manufacturer is not responsible for the goods during delivery.
FOB destination means that the manufacturer owns the inventory until the buyer actually receives the merchandise.
Above when we discussed work-in-process, we mentioned direct material and labor costs, as well as overhead costs.
Direct material costs include anything that is used specifically for your product. In our example above, this would include the metals and motherboards. As with other industries, manufacturing also has a direct labor cost. These direct labor costs would include anyone on the assembly line that is putting your computer together.
To determine direct costs, a manufacturer can either use standard costing, weighted average coast, or the cost layer method. As we stated in our ‘Bookkeeping for Manufacturing Businesses’ blog, standard costing is one of the more common costing methods used in manufacturing. This method simply establishes the standard rates for materials and labor used in the production of your goods.
There are also indirect costs, and this could include any indirect materials, such as screws that the company purchases in bulk and does not assign to specific inventory. There is also the expense of indirect labor, such as supervisors or support staff that needs to be taken into consideration.
A manufacturing company will have overhead costs as well. These costs need to be added together, then allocated to the number of units that are being produced within a specific reporting period. This is an important cost to remember and needs to be added to the cost of inventory.
This includes costs that are associated with the manufacturing plant itself. This would include any building maintenance, taxes, insurance, utilities, deprecation, and so on.
All of these various manufacturing costs associated with your inventory are considered product costs.
Your inventory and product costs are listed as current assets on your balance sheet.
Whether your inventory is considered to be a raw material, work-in-process, or finished good, they are all still assets. On the balance sheet, they would be placed into the inventory account that they are currently associated with at that time in the manufacturing process.
When these goods are sold, they are transferred out and recorded in the cost of goods sold account. This account represents the product costs of all of the goods sold during the period of time in question.
Your bookkeeper or accountant will need all of these amounts, including the raw materials for production, the cost of goods manufactured, and cost of goods sold in order to prepare the income statement.
There are schedules that are created, so that the allocation can be easily seen. The three schedules include the schedule of raw materials, the schedule of work in process and the schedule of cost of goods sold
Each schedule is required in order to fill out the next schedule. To make better sense of the schedules, look at the inventory cost flow equation that is used for each.
Beginning inventory + purchases = cost of goods available for sale
Cost of goods available for sale – ending inventory = cost of goods sold
As an example:
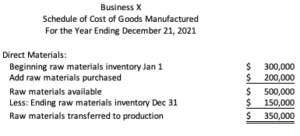
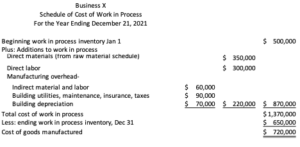
Some may then add an additional schedule, combining the schedule of cost of goods manufactured and the schedule of work-in-process, or they may simply go on to the schedule of cost of goods sold.
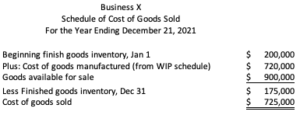
These schedules are typically created for internal use, and only the income statement is shared.
The information that is transferred on to the income statement looks like this:
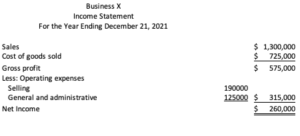
As a final note, we want to briefly touch on Inventory management.
Having inventory for too long of a period of time, isn’t good for a manufacturing business. There are not only the concerns over any increases in storage costs, but there is also threat of the goods becoming obsolete while sitting in storage.
On the other hand, having too little inventory also has its share of problems. You may run into issues with the supply chain system, that would then cause the manufacturer to not only lose the profit from potential sales, but they may start to lose market share over time.
Or as a manufacturer, you may decide to have your product go out on consignment if it is more specialized, or not you don’t have a high volume of product. Consignment is when the producer decides to partner with a retailer. The producer owns the product, or inventory, but it is held by the retailer.
Once a customer chooses to purchase this item, the retailer will purchase the item from the manufacturer. The benefit to the manufacturer is that their product is being promoted to an end user. The downside may be that their product is in their inventory for an extended period of time.
How best to manage your inventory is something worth discussing with your bookkeeper or accountant.
Need help from an expert?
We know that this can be complicated. Let one of our experts at Valley Business Centre help. For over 30 years, Valley Business Centre has been providing comprehensive bookkeeping, payroll and tax services to our clients in Whistler, Squamish, the Sea to Sky Corridor and metro Vancouver B.C. areas. Valley Business Centre provides reliable and effective services to all clients.
Disclaimer
This article is written for informational purposes only. It is current at the date of posting and changes to laws and regulation may result in the information becoming outdated. It is not intended to provide legal, tax, or financial advice. It is recommended that readers get advice from a tax professional before making any final decisions.